FTL
Automates transports – Controls access – Optimizes processes
The Driverless Transport Solution – FTL from Eberle controls autonomous transport robots and thus automates transport tasks in intralogistics. FTL enables automatic communication between transport robots, the building infrastructure, manufacturing equipment such as machines and plants, and the enterprise resource planning (ERP) level.
FTL increases the reach of driverless transport robots. Through dynamic driving orders, it controls the optimal utilization of the entire fleet. As a control program, the FTL management system guarantees a safe and stable flow in the transport chain and automatically controls transport orders, handling and access authorizations of the robots in the individual areas.
Driverless Transport Solution
Autonomous driverless transportation systems
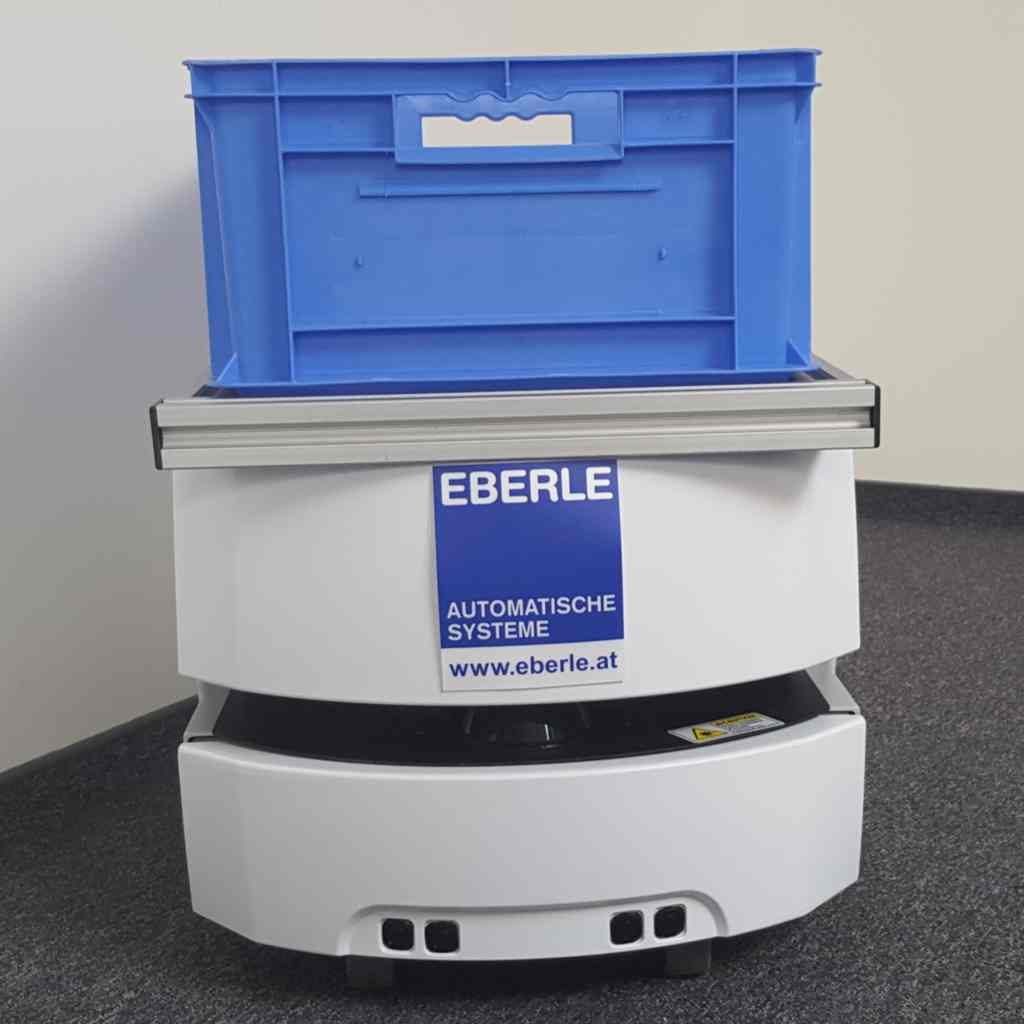
The basis of any FTL solution is autonomously navigating transport robots. These are able to orient themselves independently on the basis of surrounding structures and detect obstacles in the route via the integrated sensor technology. The transport robots calculate their position independently and plan the route to the destination automatically. Transport robots relieve employees and make intralogistics efficient and highly available.
FTL clears the way
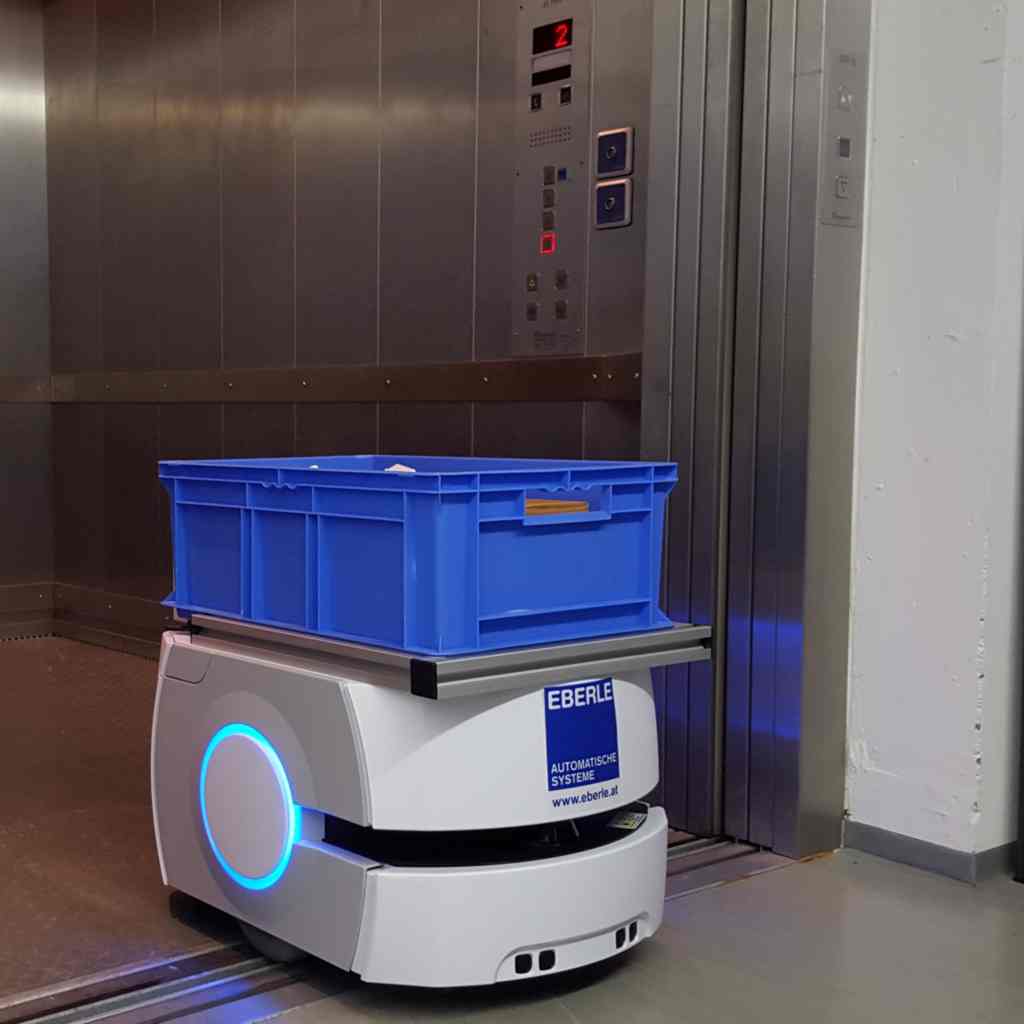
Autonomous transport robots navigate independently, but by default they cannot overcome structural obstacles such as locks, doors, gates or elevators. For communication between the transport robot and the structural barrier, it requires a higher-level management system that, for example, opens doors and regulates access.
The driverless transport solution – FTL from Eberle establishes communication between the transport robot and the structural barrier. FTL thus increases the reach of transport robots across locks, access points and floors.
Automated material flow
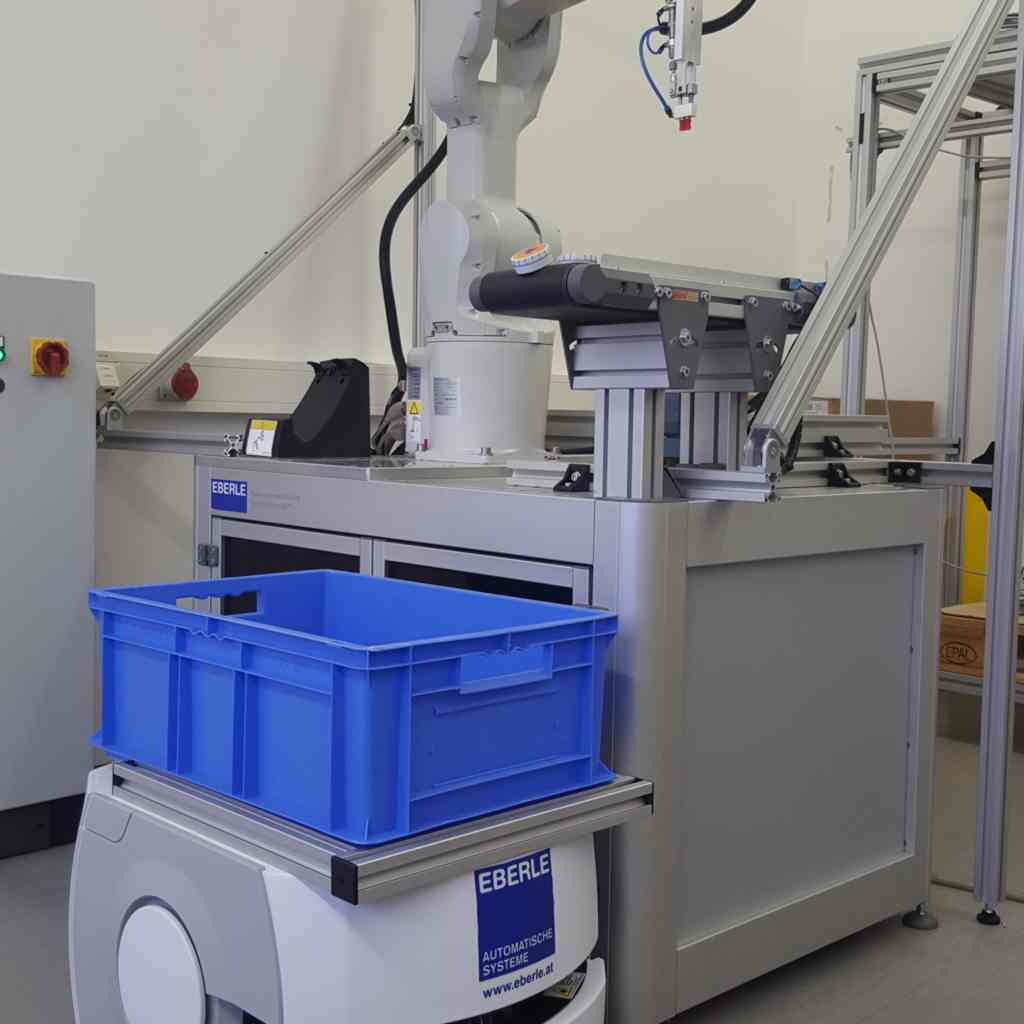
For loading and unloading machines, FTL provides the interface to automated interlinking for material flow control. When a batch size is reached, for example, the machine sends the order for the removal of the goods to the FTL system. The system checks which transport robot from the fleet is available in the immediate vicinity and transmits the transport order to it.
FTL ensures smooth transports, avoids congestion and continuously guarantees material availability at the machine. In this way, FTL increases the degree of autonomy of plants. Continuous and automatic data recording makes transport processes transparent and traceable.
control – request robot mobile
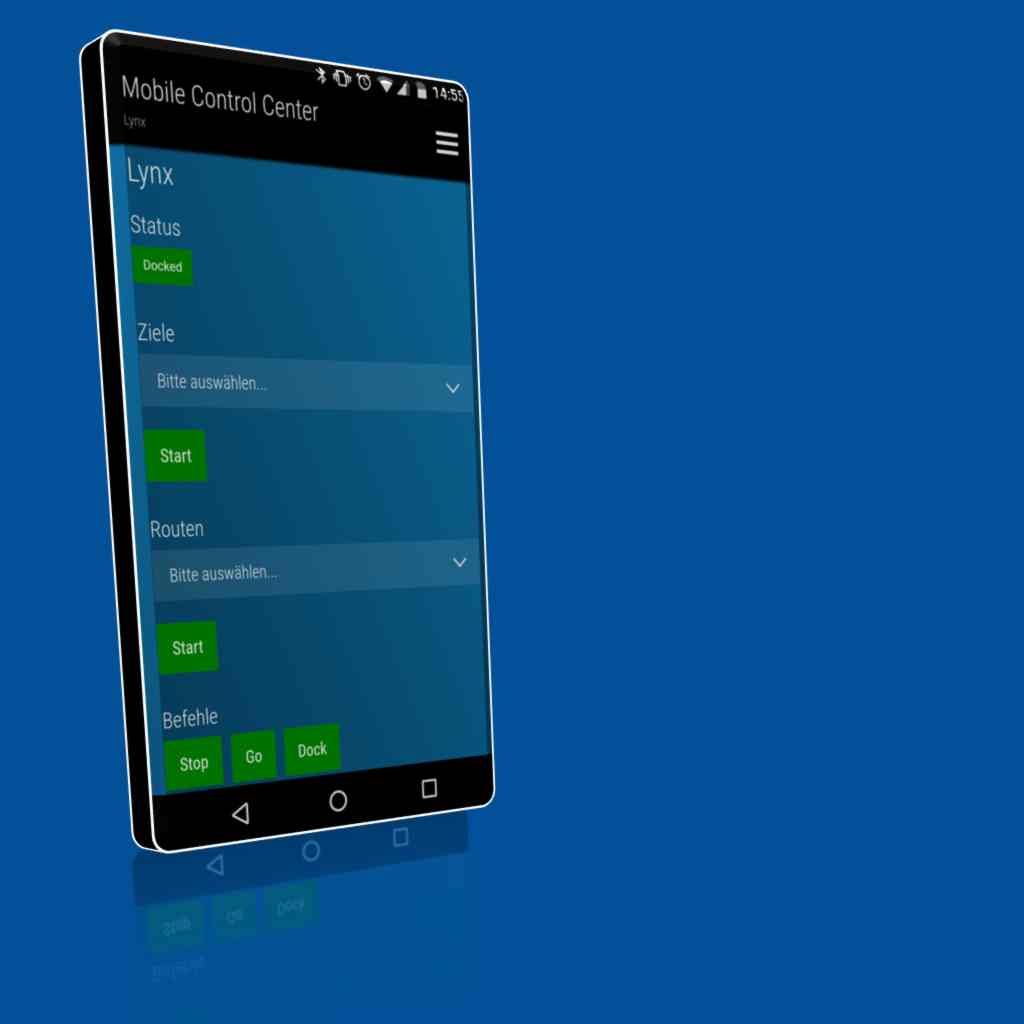
For manual workplaces or sporadically needed transports, FTL in combination with control offers the possibility to request a transport robot using mobile devices. For example, an employee can enter the pickup location and specify a route via the control web application on a cell phone. FTL receives the transport order and organizes the pickup.
FTL makes transport robots flexible and guarantees an optimized material flow at the workplace. Automated deliveries and removals relieve employees and free up resources for core staff tasks.
Vertical integration for FTL
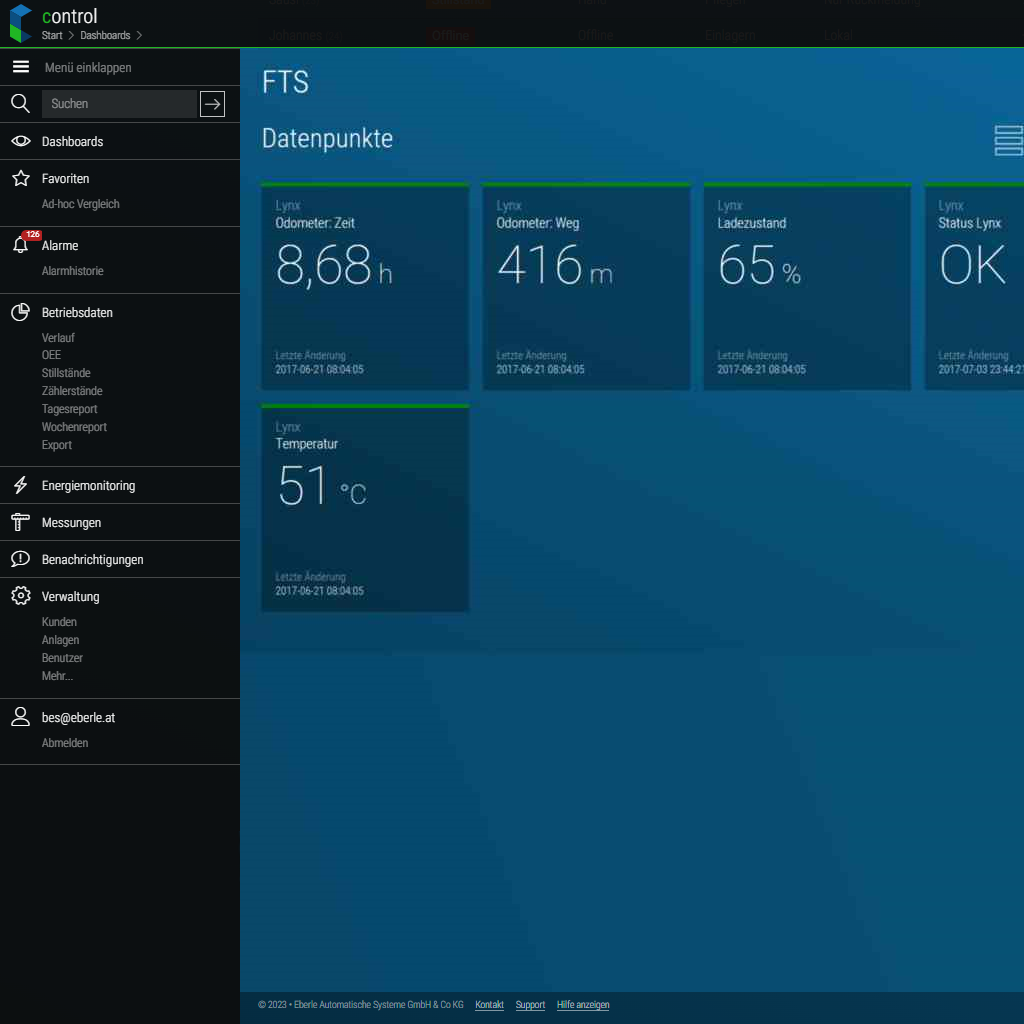
The IoT platform control links the automated guided vehicle solution FTL with the enterprise resource planning (ERP) level. On the one hand, the control serves as a data interface between ERP and FTL, and on the other hand, it also enables the manual input of transport orders. The control takes over the operative robot data from the FTL and stores them continuously and continuously for the production data acquisition. Company-wide information on transport orders, status, maintenance information, etc. is available at any time via the control web application.
control and FTL automate intralogistics from the highest corporate level. Transport tasks thus become consistently transparent and can be linked directly to order processing, for example. Transport processes in intralogistics are traceable at all times.
Demovideo
FTL, AGV and control in practical application. FTL manages the automatic removal of material as well as navigation over several floors and the outdoor depot.