Robot Automation
Robots are widely used in industry today and have many applications. Robotics is one of the cornerstones of Industry 4.0, and in the smart factory of the future, the flexible use and rapid adaptation of machines is critical to success.
Robotics can best meet this and other requirements such as high availability, inhuman working environments, high precision and repeatability.
The ability to work together with humans “safely” is what particularly distinguishes robots. With the new generation of collaborating robots, previously unimagined approaches to solutions are emerging. This is how humans and robots are now going “toe to toe.”
Robot Palletizing
Packed on or off – Fast – Strong – Reliable – Tireless
Palletizing can easily be carried out via several infeed sections or palletizing stations and with different containers such as crates and cartons.
The integrated barcode scanner enables clear identification of pallets and goods.
Different pallet formats and several transport units can be gripped simultaneously. Empty pallet and layer pad handling is automatic.
The system can be fully integrated into pallet and carton conveyor systems.
Gripper types
Universal gripper – Magnetic gripper – Carton gripper
Complete palletizing cell
Solution example
Technical data
- Palletizing robot with base and carton gripper
- up to 10 cycles / minute depending on the carton and palletizing pattern
- Carton size from L300*W200*H80mm to L300*W400*H300mm
- Stacking height up to 1600mm
- Carton weight 1 to 20kg
- 3 carton types and 3 palletizing patterns
- Centering stop for euro pallet
- Safety barrier with safety door
- I/O interface to on-site carton conveyor system
- Control cabinet with touch screen and control panel
- Stack control computer incl. parameter and alarm management, manual operation
- Space requirement approx. 3*3*3m
Robot Reach into the Box & Separation
Recognizes – Arranges – Adjusts – Calculates – Plans – Accesses – Provides
Bin Picking (Reach into the Bin)
Workpieces as bulk material are detected with a high-resolution optical method. The information thus obtained about the position and orientation of the workpieces is transmitted to the robot. The integrated path calculation module takes into account gripping point and interfering edges.
The advantage of such solutions lies in the rationalization of processes. With low costs and space requirements, an increase in autonomy time is achieved. In addition, camera measurement guarantees exact part placement. The targeted “reach into the box” incidentally also causes no significant noise.
Sorting
Regardless of how the workpiece is fed, the robot detects position and identity with an integrated camera system.
A high-resolution industrial camera is used to determine the position and measure the objects. The robot picks up and aligns the workpieces.
Thus, for example, the loading of machine tools runs completely automatically.
Application video Bin Picking (Reach into the box)
Robot & Machine
Loading – Unloading – Control
In machine interlinking, the robot supplies fully automatic production machines or conveyors that are in production. Whether feeding or discharging material in the production process, the robot can be used bidirectionally. During filling into the transport containers, a production control is carried out fully automatically by means of a camera.
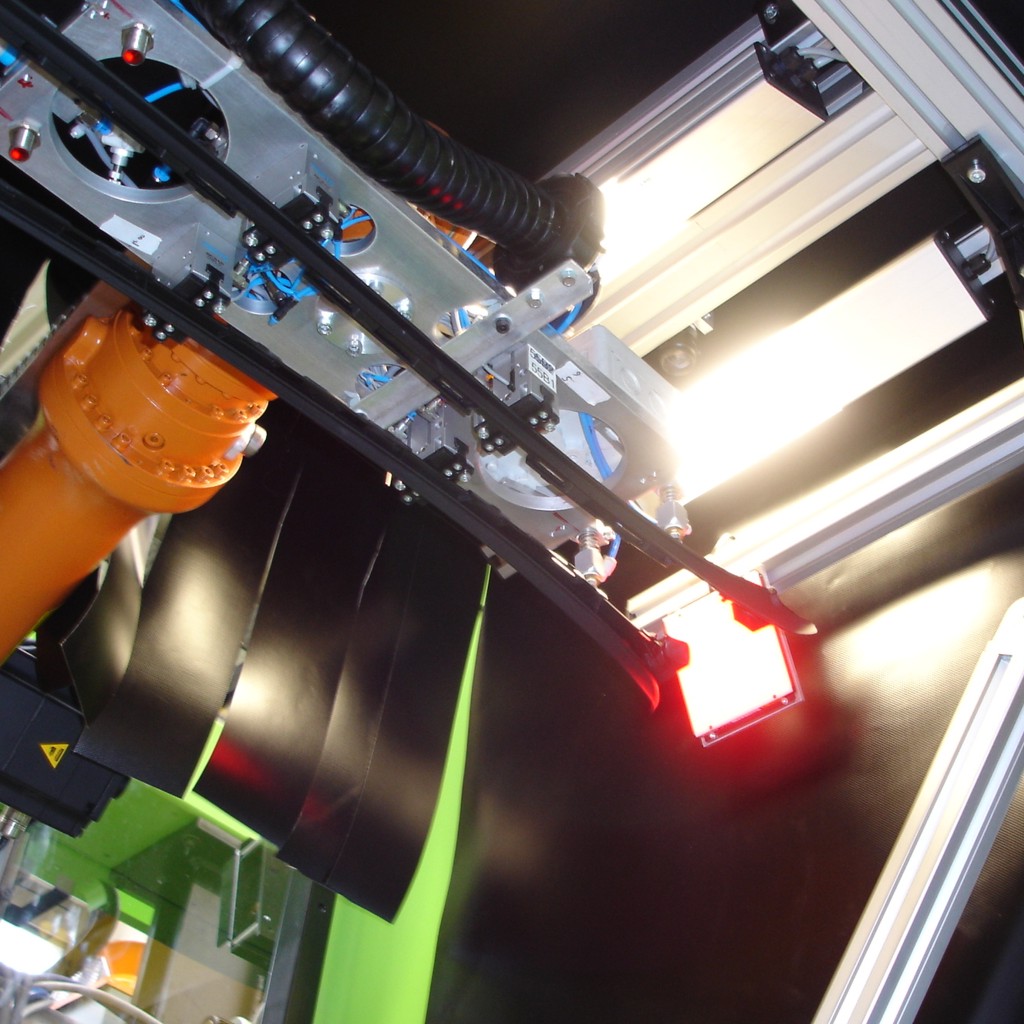
Roboter Pick & Place
Small – Precise – Fast
For Pick & Place solutions, SCARA robots and camera systems are used. The SCARA robots meet the highest standards of precision and speed. As the fastest in their class, they master even the most complicated tasks in the tightest of spaces. When it comes to the rapid handling of small components, they are therefore the first choice.
Applications
- Highspeed Pick & Place
- Fine assemblies
- Material handling
- Packing
Technical Data
- Reach from 600 to 800 mm
- High resolution camera system
- PC-based image processing and data input by host computer
- Transmitted light illumination integrated in the belt
- Position and orientation of the parts in high accuracy
- Quality control of the parts
Robot & Human
Emotive – Sensitive – Precise – Safe – Collaborative
Responsive, collaborative lightweight robots let humans and robots work hand in hand. With the intelligent assistant, a wide range of possibilities opens up for relieving work areas or automating repetitive manual work. The flexibly deployable ‘digital colleagues’ score with precise repeatability and enable the implementation of cost-efficient robot solutions.
The sensitivity of a cobot overcomes the barrier between man and machine and allows cooperation without protective enclosure. To ensure safe cooperation, special rules apply to collaborative robots. These are defined in the ISO standard (TS 15066). For example, the device for gripping must also be collaborative. Additionally, system integrators use a risk assessment to determine whether the limits are met in the event of accidental contact.
Autonomous transport robots
Autonomous – Flexible – Reliable
Driverless transport solutions from Eberle are integrated into existing infrastructures.
With autonomously navigating transport robots and a higher-level
management system, transport tasks in intralogistics are solved. The areas of application are diverse and take on tasks ranging from warehouse logistics to automated machine linking. In extensive production facilities and plants, the internal transport of goods is organized.
Thanks to intelligent sensor technology and computer-supported autonomous navigation, the transport robot moves safely during ongoing operations. If an unexpected obstacle appears, it recognizes this and independently searches for an alternative route. Desired routes and drivable areas can be specified in the software. The transporters overcome structural obstacles such as gates, doors and elevators. The transport robot receives authorization to pass through passages or request elevators from the higher-level control system.
With a fleet management system, transport robots can be used even more flexibly. Here, transport orders are sent to the control system, which then organizes the automated transport from A to B.
Technical data of mobile transport robots (example)
- Load capacity for a payload of up to 60 or 90 kg
- Battery with 60Ah for an average runtime up to 13 hours
- Speed max. 1800mm/s
- integrated voice and audio output